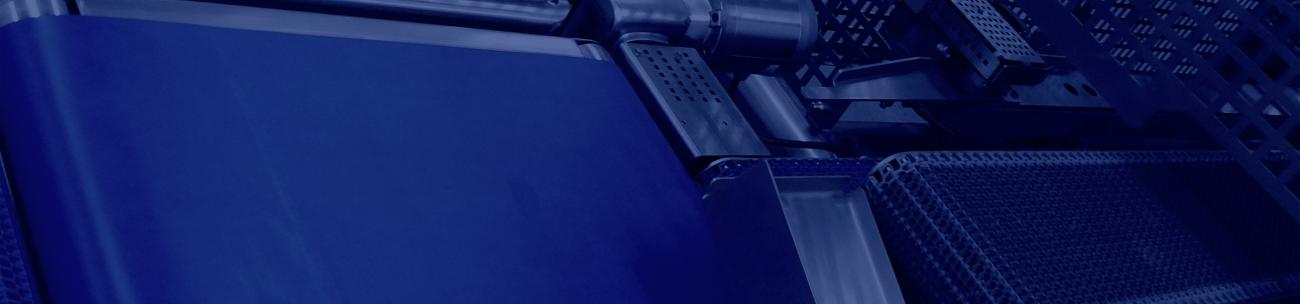
Tray padding is one of the key components in consumer meat and poultry packaging. We offer a proven high-speed solution for padding trays and our equipment can be designed and engineered for a wide range of products. This machinery reduces the human workforce needed for the process, resulting in lower cost output over time, fewer work-related injuries, and an increase in your bottom line.
Model 357HS Pad Placer
Our pad placer unit is a high-speed solution to apply absorbent soaker pads into consumer trays. This unit operates in-line with the tray manufacturers thermoforming process.
The tray feeder unit accepts stacks of trays and feeds the tray denesting unit. Our pad placer unit utilizes our Model 125 tray denester to separate vertical stacks of trays and feeds them onto a flighted chain deck. As each tray exists the denesting unit, a programmed amount of adhesive is applied to the bottom of the tray.
After the tray passes through the Nordson Pro-Blue Flex glue system, which uses the Nordson Eclipse glue pattern control with dual glue heads for application, it is then transported to the pad application unit. A continuous roll of padding material, supplied via rolls or bulk gaylord container, is then cut to a predetermined length and applied to the tray. This length is determined by the size and shape of the tray and set through the operator interface.
Once completed the trays pass thru an optional bottom label station which, if needed, will apply pre-printed labels onto the bottom of each tray. The final step in the process is the renesting of the trays. The renester accepts the trays and rotates them to a vertical position where they are to be stacked horizontally on the packaging table.
Equipment Specifications
- Typical tray throughput rates up to 250 trays per minute. Speed rates are directly dependent upon tray denesting qualities. Tray evaluation will determine expected throughput rates.
- Tray padding for trays with maximum tray depth of 2.5”.
- Unit capable of processing clear, white, yellow, black and rose-colored trays.
- Padding mechanism capable of processing either registered pouch pad or ply padding material up to 13” width with the 14” wide knife. Pad placement within tray may be controlled via the operator interface. Electronics capable of processing yellow, white and black padding material.
- Three axis integrated servo control system – driveline, film drive and knife mechanism.
- Allen-Bradley Electronics and PanelView Plus color touch screen operator interface.
- Nordson ProBlue 10 glue system.
- Nordson Spectra glue pattern control.
- Nordson dual glue heads deliver glue application.
Options
We offer many different options on our Pad Placer equipment. Our most popular options are the film drive assist, bottom labeling, and metal detection.
Bottom Labeler
Supports only preprinted labels for tray bottom application. Subsequent installation of bottom labeling option will require modifications or installation of flight drive chains and tray deck. Please note, all Model 357HS Pad Placer frames are manufactured to accept the bottom labeling option. Modifications required are limited to tray movement area. Subsequent installation of bottom labeler will incur additional modification charges and the unit would need to be returned to Waldrop for labeler installation and modifications.
Film Drive Assist
To assist customers utilizing continuous roll padding – supplied via bulk gaylord container, a film drive assist mechanism is offered. This assist mechanism provides for a smooth pad transition between the container and the registration film drive of the Model 357HS. Primarily, this assist mechanism eliminates the tension on the registration film drive thus eliminating slippage introduced by the weight of the padding material.
Assist film drive is an additional servo axis, integrated within the Model 357HS controls package. As drive is defined in the motor ring, speed requirements are matched to the operation speed of the padding equipment.
Metal Detection – Pad Material
Metal detection equipment to continually inspect padding material prior to padding operations. Quality insurance check provides for machine shutdown on detection of metal particles within padding material.
As a leading manufacturer of complete and customized automation systems for food processing and packaging companies for over 60 years, our proven goal is to decrease the reliance on outdated manual processes to reduce operation costs and improve overall operation efficiency.
With adequate information regarding your needs, we can help customize our Pad Placer equipment to ensure you get the highest possible efficiency with the lowest amount of risk.