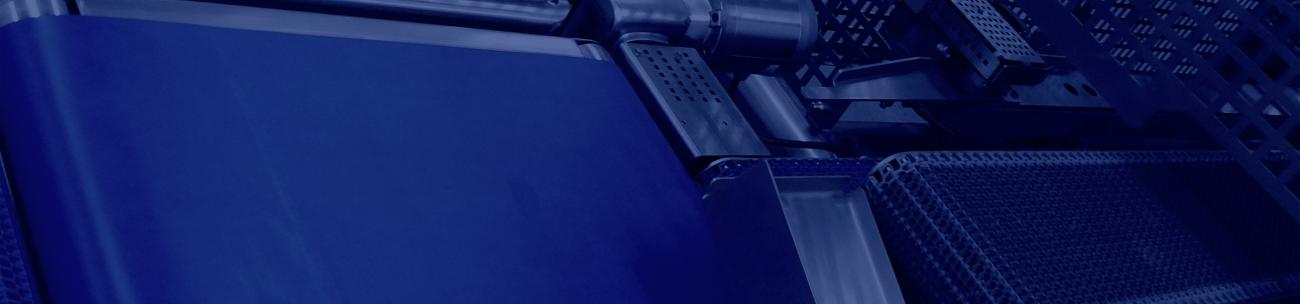
Waldrop manufactures a wide range of robotic casepacking systems tailored to your specifics products. The primary goal of the robotic casepacking is to increase efficiency and capacity of the process while offering labor savings. As an ABB Robotics integrator, we are able to utilize their robotics within our equipment to provide a seamless solution for your application.
In addition to the ABB Robotics used within our Robotic Casepacking systems, depending on the products, we will design a custom end of arm tooling to accommodate your package format. Most of our Robotic Casepacking systems include an infeed conveyor with encoder tracking. Product tracking is accomplished with the ABB IRC 5 robotic controller which provides accurate product picking for packages entering the workcell. A case conveyor presents empty cartons or cases for casepacking operations. Encoder tracking provides case placement data to ABB IRC 5 controller for accurate product placement.
As an option we offer infeed quality control inspection. Prior to product entering casepacking workcell, all parts are positively identified for appropriate top and bottom labeling. All parts are required to contain product identification top labeling & contain bottom labeling which includes a 1D bar code. Top label inspection is completed via vision inspection – Cognex vision sensor. Any parts with unreadable or improper top or bottom labeling are identified as incorrect and not included in any pick and place casepacking operations. Those parts identified with improper labeling are passed through workcell to customer supplied rework container.
Robotic Casepacking system is controlled via Allen-Bradley color touchscreen operator interface. This provides recipe selection, unit feedback and control information. This coupled with Allen-Bradley CompactLogix PLC and associated components provide a quality solution you can count on. With Allen-Bradley products on each and every piece of machinery, you’ll receive data in real time to help you maintain quality, efficiency, and profitability.
Our standard Robotic Casepacking systems include several high-quality products, including:
- ABB Robot with panel mounted IRC 5 robotic controller.
- Allen Bradley controls with color touchscreen operator interface.
- Stainless Steel Motors & Reducers (where applicable)
- Intralox and Habasit Belting Options
- Hoffman Watershed Enclosures
- IP69K Push Buttons, Switches & E-Stops
Our building standards include:
- Hygienic design for food production applications
- Frame is continuous TIG welded 304 stainless steel
- Stainless steel grade 304 – 1.25” bore solid shafting
- Solid belt wear bars
- Stainless steel bearings and end caps
- Stainless steel threadless support leveling feet
Many of our Robotic Casepacking Systems can be combined with other product offerings. For instance, the empty case conveyor could provide pre-built boxes supplied by a box erector on a conveyor system to speed the process as much as possible. Completed cases exiting the system could then also be carried away through a separate conveyor system to the next step of your manufacturing process such as case checkweighers, rejects, case labeling, case sealing equipment, robotic palletizing systems, stretch wrappers, etc. Upstream we offer tray denesting, product loading, metal detection equipment, etc. to decrease the manpower needed to complete the project.
What really sets Waldrop apart from other food production and packing automation machinery providers is our design standards and the technology included to help you increase efficiency and decrease downtime. With the primary goal to increase efficiency and capacity while saving money on labor – our robotic casepacking equipment is a perfect solution.
Regardless of where you are in the casepacking process, we are here to assist.